表面レーザテクスチュアによる摩擦制御
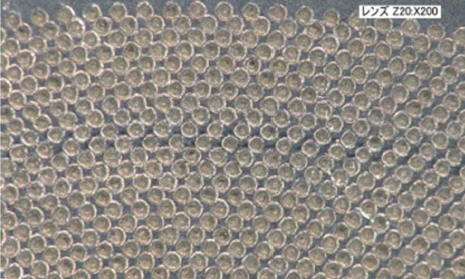
トライボロジスト第65巻第5号掲載
<特集>表面テクスチャによる摩擦制御
表面レーザテクスチュアによる摩擦制御
―超短パルスレーザ微細加工―
井ノ原忠彦,相澤龍彦
Process Tribology Control by Laser Surface Microtexturing
―Short-Pulse Laser Microtexturing―
Tadahiko INOHARA and Tatsuhiko AIZAWA
Abstract
Picosecond and femtosecond lasers have grown up as a powerful and reliable means to make micro-drilling, precise shearing and micro-texturing. In particular, the laser microtexturing has been widely utilized to form the regularly aligned micro-dimples even in the inner surface of cylinder block liner as well as the piston skirt for significant reduction of friction and wear. This technology was also available to improve the machining tool life by trapping the machined debris into micro-pockets. In addition, the laser micro-/nano-texturing worked to control the surface properties; e.g., the hydrophilic stainless steel surface was changed to be super-hydrophobic. Furthermore, with aid of the low temperature plasma nitriding, the micro-/nano-textured tool and part life could be prolonged in practical applications.
Key Words : micro-dimples, micro-pockets, friction, tool wear, engine parts, surface property control, low temperature plasma nitriding.
1.はじめに
我が国産業では、一層の省エネ・省資源に加えエネルギー分野での火力発電等によるCO2排出量増加を補填する技術が必要とされている.
摩擦係数低減はその有力な技術の一つであるが、すでに回転部、摺動部などに、マイクロテクスチュアを施すことで摩擦抵抗・摩耗を減少させる技術は、あらゆる研究機関・企業で研究されている.しかしながら、均一な性能と一定の品質を確保するための正確で規則正しいマイクロテクスチュアの形成は今までは困難であった.
そこで、バリなどを排除し、高硬度材(材料を選ばない)への微細で高精度の加工技術が、高速で可能になれば、従来の加工技術では実現不可能なマイクロテクスチュアによる表面機能向上が期待できる.それらを解決するために、レーザの応用が叫ばれて久しいが、近年ピコ秒、フェムト秒と呼ばれる超短パルスレーザの出現により、熱影響による形状不整を解消することができるようになり、機械加工と遜色ない加工面と、より微細な形状を高速で得ることができるようになった.
その理由は図1に示すように、パルス幅(レーザが1回発振している時間)が、ピコ秒(10-12秒)、フェムト秒(10-15秒)と短いためである.
1ns(ナノ秒)のパルス幅を持つレーザのピークパワーが1mjあたり1MWであるのに比較して1ps(ピコ秒)レーザは1GWのピークパワーが得られ、今までの光と熱による加工から、光によるアブレーション加工に変化し、熱影響のない清浄な加工面が得られるが、加工速度は明らかに遅くなる. しかし、短パルスであるがゆえに、高繰り返し周波数を得ることができる.現在では40 MHzのレーザも出現しており、それらのレーザ能力を、完全にコントロールすることができれば、すなわち高速で移動する光走査機構もしくは、高速で移動するアクチュエータとの同期連動が可能になれば、高速化は可能になる.現在では200 m/sの操作速度を実現している.最速スキャンスピード200 m/s とは、時速換算720 km/h であるから、国内線ジェット機の巡航速度並みである.この時、レーザ周波数を例えば8 MHzに設定すれば、ドット間隔は0.025 mmになり、イメージするならば、ジェット機に搭乗しながら光の礫を25 μm間隔で地上に正確に並べていることに匹敵する.図2にガルバノスキャナとポリゴンスキャナの比較を示す.
これらの技術は、金属加工業界においても、プレス金型、切削工具などへマイクロテクスチュアを施すことにより、工具の延命化、加工油の軽減、洗浄工程の簡略化が期待できる.
2.超短パルスレーザでの微細加工
超短パルスレーザは、分子レベルの化学初期反応持続時間程度のパルス幅であるため、その間での非加工材のアブレーションにより、熱的プロセスを伴わない加工ができることが最大の特徴である.その原理は今まで想像もできなかった微細形状を種々の材料に付与することを可能にし、加工工具を用いないため、数十μmレベルの微細なパターンをバリ、だれ無しで材料表面に付与することができる.
これらの微細パターンは、高硬度の金属表面であっても、又、DLCコーティングや後述する窒化処理などの高硬度表面であっても、熱影響を受けやすい樹脂材料であっても、その加工性は良好である.
まず、孔加工とテクスチュア加工例を紹介する.
2.1 孔加工技術
一般的な常識では、レーザ光のガウシアン形状に伴い、単調にレーザ光を照射した状態では、テーパ形状となりテーパの角度は制御不能である.
図3は、独自の光制御機能を用いてテーパ制御した加工写真である.特筆すべきは、まったく熱影響が見られず、テーパ角度が制御可能となったことである.当然のごとくドリルと同様のストレート穴加工も可能である.そのため機械加工では困難な高硬度金属材料、セラミックスなどへの微細穴あけ加工が可能となった.最小加工径はφ10 μm、アスペクト比は10倍を実現しており、真円度も良好(1μm以内)である.
2.2 切断
超短パルスレーザにおける金属切断では、熱応力が発生しないため箔の切断などには最も有効でありエッチングでは寸法確保が困難な高精度加工に多く利用されている.又プラスティックスの切断に於ける利点は、切断時に発生するプラズマにより溶融したカーボンなどが、切断面及びその周囲に付着しないことである.そのため、化学処理などによる後工程を全く必要としない.特に一般的なポリマーに加えて、熱に弱いとされる生分解性プラスチック、微細加工は不可能とされたフッ素樹脂、CFRPのような複合材であっても、高精度の加工が可能となった.
2.3 微細形状創成
超短パルスレーザは、種々の光学系・ビーム制御系の工夫により、適切な除去加工パス、加工エネルギーで微細形状の付与が可能になる.図4、図5、図6に、創成された微細加工の一部例を示す.図7に於いては、ピット加工例を示している.
レーザ加工条件の最適化は、あらゆる形状の創成を可能にし、しかも対象の材料を選ばず、高硬度の材料への微細形状付与が可能であり、加工例を見ても、極めて規則正しく配列されていることがわかる.
3.レーザマイクロテクスチュア技術とその応用
材料表面に正確で規則正しい微細な構造を付与することにより、高度な機能が発現されることが証明されている.基本機械部品の摩擦係数低減や、切削・プレスなどの加工工程の改善に応用されている.
ここでは、その応用例を紹介する.
3.1 マイクロテクスチュアの摩擦係数低減技術
トライボロジーの世界では、長年にわたり表面機能向上による摩擦係数低減が研究されてきた.潤滑油を使用する場合の一般的な理論は、摺動時の2物体間において、摺動速度が遅くなると、それぞれに折衝状態となるスティッキング現象が生じる.この不具合を解消するためには、2物体が接近しても、薄い油膜面が形成されている必要がある.すなわち、摺動する2物体間が比較的大きな圧力バウンダリーになっても、接触をさけることができれば、摩擦係数の急速な増加は回避される.そのために、微細構造を持つマイクロテクスチュアを付与し(いわゆるミクロプール、微細な油だまり)形成された薄い油膜により2物体間の接触を回避する技術である.しかし、正確で規則正しく、且つ微細なミクロプールを高速で付与することができない限り、実用化には難しいものがある.
図4に示すディンプルは、金属材料表面に付与されたミクロプール形状を示す.まったくバリなどの発生が無く、正確な開口径、正確な深さと曲率、正確なピッチで付与されている.特に、設計された機能を確保するための精密に仕上げられた部品表面の精度、表面粗さは、そのまま確保されているため、テクスチュア付与により部品の仕上がり表面に影響を及ぼすことはない.図8には、テクスチュアを付与した際の摩擦係数比較を示す.
これらは、軸受などに限らず車のエンジン周辺やその他の回転部、摺動部への研究も進んでいる.図9に、シリンダブロック・ライナー内面への加工例を示す.図10は、ピストンスカートへの応用例である.ともに規則的にマイクロディンプルが形成されていることがわかる.
3.2 マイクロテクスチュアの切削工具への応用
ここでは,文献に示す、マイクロテクスチュアの切削工具への適用事例を述べる.
これまでは、切削工具表面は可能な限り平滑に仕上げることが、一般的な考え方であった。しかし、前述したように、レーザーマクロテクスチュアにより、種々のパーツ表面に、内面か曲面に関わらず、またその材質によらずに、規則的な配列で設計したマイクロテクスチュアユニットを加工でき、またマイクロテクスチュア表面における摩擦係数が大幅に低下することから、新しい方向性が見えてきた.
切削工具の表面を、可能な限り平滑に仕上げるという既成の知見とは全く逆に、積極的に、工具表面にレーザマイクロテクスチュアを付与することにより、様々な機能を発現する切削工具の開発が進んでいる.
ここでは、切削工具にマイクロディンプルを格子状に配置した工具を開発し、従来の平滑面からなる切削工具との比較を行った9).
炭素鋼の切削加工実験の一例を図11に示す.同一加工条件下での通常の工具と、ディンプル構造を付与した開発工具の摩耗量に及ぼす影響を示したものである.この切削事例においては、マイクロテクスチュアは工具と切りくず界面への切削油剤を保持するオイルプールとしての効果、摩耗を促進する硬質摩耗粒子をトラップするポケットとしての効果を発現することで、工具摩耗を抑制している.工具の最大クレータ摩耗深さを比較すると、開発工具に於いて60%摩耗が抑制されていることがわかる.
Al合金のドライ切削加工実験の一例を図12に示す10).同一加工条件下での通常の工具と,テクスチュアを付与した開発工具における,切りくず凝着の量を示したものである.この例では、加工中に凝着物生成と脱落が繰り返される.耐凝着性向上のためには、いかに構造内部への切りくずの侵入を抑制し,脱落を促進するかが重要となる.
図13はテクスチュア構造と凝着物の比較を示している.溝構造の場合,切りくず流出方向と溝方向が一致する場合,通常工具以上の凝着が発生することが明らかとなり,極めて強い方向依存性を有していることが確認できる.したがって,複雑形状加工など,切りくず流出方向が常に変化するような加工において凝着を抑制するためには,ディンプル構造などの方向依存性が少ない構造が有効となると言える.
以上のように,工具表面に形成されたマイクロテクスチュアは、工具と切りくず界面において切削油剤を保持するオイルプールとしての効果9, 11-13),切削油剤の微細流路としての効果14)、凝着物の脱落推進効果10)、接触面積の低減効果12, 14)、摩耗を促進する硬質摩耗粒子をトラップするポケットとしての効果9, 13),凝着物へのアンカー効果15)など、切削加工中に様々な効果を発現することが明らかとなっており、それぞれの現象の組み合わせによる切削条件の確立が重要になってくる.
4.その他の表面機能向上
フェムト秒レーザパルスをアブレーション閾値近傍のフルエンスで照射すると、入射光の偏光方向と垂直の方向に、レーザ波長と同程度、またはそれ以下のナノレベル間隔を有する周期構造が形成されることが知られている.この微細周期構造はLIPSS(Laser Induced Periodical Surface Structure)と呼ばれている.その応用については、摺動部の摩擦・磨耗低減などが挙げられている.しかしながら、その応用研究は、 必ずしも十分になされているわけではない.
4.1 LIPSSにおける撥水効果16-18)
図14は、LIPSSが、超撥水効果を発現し、純水に対する通常のステンレス表面とLIPSS加工された表面との静的接触角の比較である.接触角は、70°から150°に向上している.
5.レーザマイクロテクスチュアの摺動時の課題
回転部や摺動部の長時間での過酷な稼働では、付与したマイクロテクスチュアの摩耗による消滅も考慮する必要がある.そのためには、機械部品基材・金型工具基材などの硬度・耐摩耗性も合わせて高度化しなければならない。一方、高温熱処理あるいは一様な表面処理では、熱ひずみによる形状寸法の不整の導入あるいは表面処理による表面機能喪失のリスクも発生する。金属基材元素の拡散が生じない低温での処理19-20)あるいはマスキング技術を併用した選択的な表面処理21-23)が必要となる。
ここでは、著者らが提唱している、低温プラズマ窒化とレーザマイクロテクスチュアの組み合わせによる研究を含め、レーザマイクロテクスチュアの摺動時の課題解決法を考える。
5.1 低温プラズマ窒化
文献20、24)で紹介しているように、ステンレス鋼材では、鉄・クロム・ニッケルなどの構成元素の拡散が生じる、保持温度が主として500℃以上の高温域を利用するプラズマ窒化(以下、高温プラズマ窒化)と、ステンレス鋼材構成元素と反応しない保持温度が主として400℃以下の温度域を利用する低温プラズマ窒化がある。前者では、構成元素と表面から拡散する窒素原子との反応が生じるため、基材中の窒素濃度はFe-N系状態図の最大窒素固溶量(0.1-0.2mass%)程度であり、母材にCrNあるいは鉄系窒化物が析出した微細構造となる。表面硬度は1200HVに達するが、クロム濃度が析出反応により低下するため、腐食を伴う摩耗摩擦環境では劣化が進行する。析出物が疲労クラック生成を誘発するため、過大な繰り返し負荷に対しては、耐久性低下が危惧される。
低温プラズマ窒化では、鉄・クロム・ニッケルと拡散してきた窒素原子とは直接反応せず、窒素固溶原子はステンレス鋼結晶子の8面体空隙に侵入占有する。この窒素合金化に伴い、結晶子は膨張し、その弾性ひずみエネルギー密度で相変態を生じるとともに、窒素合金化した部位としていない部位のひずみ不適合を駆動力として塑性ひずみも発生する19、25-28).
金型などにも利用されるマルテンサイト系ステンレスSUS420材を例にとり、400℃4時間の低温プラズマ窒化を行い、断面組織と窒素濃度分布を調査した30).
図15に示すように,表面から一様に平均濃度 5 mass%で窒素が過飽和固溶しており,厚さ40 mに及ぶ窒化層内の結晶粒径は平均0.1 mで、微細な結晶構造となっている.このことは,粒成長と伴うような熱変形は皆無であり、しかも硬度・強度ともに増加していると考えられる。
そこで、同一のSUS420基材表面にマスキングを施し、試料表面中心の正方形部位のみがプラズマ窒化し、他の表面はマスクにより窒化を防止した実験を行った.
図16に、試料上で直交する2方向での硬さ分布を示す.マスキングされ、窒化が進行していない部位では、測定した硬度は窒化前の母材硬度である250 HVと同一である.マスキング部位と非マスキング部位との境界で、測定硬度は急峻に増加し、非マスキング部位、すなわち選択窒化部位では、平均硬さは1400HVに達する.
以上より、低温プラズマ窒化を施すことで、ステンレス鋼材中に一様に高濃度窒素を過飽和固溶させることができ、その硬度は表面のみならず窒化層領域で1400HV級の高硬度を実現できることがわかった。この窒化物などの第2相を有してない高硬度部材は、そのままでも部材摩耗および摩擦係数を減少させることができる。次に、この部材を利用して、レーザマイクロテクスチュア加工を行い、その摩擦特性を図8と同様に測定してみる.
5.2 低温プラズマ窒化と超短パルスレーザ
ここでは、SUS316基材を用い、無加工材、マイクロディンプル加工材(3種)、低温プラズ窒化材、低温プラズマ窒化+ディンプル加工材を準備し、同一条件で、摩擦係数測定履歴を求めた.
マイクロディンプルの未加工試験片では、図17に示すように、同一の潤滑条件では、表面の掘起こし効果で摩擦係数を激しく増減し、摩耗が進行していることがわかる.3種のマイクロディンプル加工試験片では、程度の差はあれ、摩耗が進行し、ボールオンディスク試験中にマイクロディンプルが消失していることが確認された.
前述したように、低温プラズマ窒化を行うと、この摩耗進行を大幅に抑制され、摩擦係数は一定となる.ただし長時間での実験では、潤滑膜の形成不良もあり、摩擦係数は増減する傾向がみられた.この低温プラズマ窒化とマイクロディンプル加工を組み合わせると、長時間摩擦試験でも、相手材による攻撃性もほとんど見られず、一定の摩擦係数で保持される.
図18に摩擦試験後の試験片表面状態を示す.SUJ2ボールとの接触があった5列のマイクロディンプルに若干摩耗した部位が認められるが、ほぼ実験前の健全性を保持しており、この低温プラズマ窒化+マイクロディンプル加工の組み合わせが、マイクロディンプル工具・金型・部品の長寿命化に寄与できることを見出した.
又、低温プラズマ窒化表面では、金属粒子が微粒子化し超短パルスレーザにおけるアブレーション加工において、場合によって金属粒子の欠けによる微小な形状不整が発生する.しかし、窒化によって微粒子化された材料表面への超短パルスレーザ加工は、特に精密ノズルのように高い真円度(0.3μm以内)を要求されるような加工には最適である.
6.おわりに
超短パルスレーザの出現は、表面機能向上の有力なツールとなりうることが証明された.その技術は、トライボロジーに限らず、バイオチップ、各種デバイス、医療用部材等多くの応用範囲が広がりつつある.我々が有する微細加工技術は、急速な発展を見せるレーザに対して、あくまでもレーザ作用点をマイクロバイトに見立て、その能力を発揮させる光学系とモーションコトロールを最適化していることであり、現在の取り組みはバイトデザインの自由化とモーションコントロール空間位置の自由化である.
【謝辞】
本解説を執筆するにあたり、杉原達哉講師(大阪大学)、の協力を得た.ここに深謝する.
【参考文献】
1) 井ノ原忠彦 機械技術(日刊工業新聞社)2017 Vol.65 No.12
2) 井ノ原忠彦 型技術(日刊工業新聞社)2020 Vol,35 No,3 p.046
3) 井ノ原忠彦 プラスティックス(日本工業出版)2017-12 p.46
4) 井ノ原忠彦 型技術(日刊工業新聞社)2017 vol.32 No.12 p.036
5) 井ノ原忠彦 相澤龍彦 塑性加工学会2017-11 C68-6
6) 平成25年度戦略的基盤技術高度化支援事業
井ノ原忠彦 相澤龍彦 「空間位相制御レーザ加工によるマイクロテクスチュア技術の開発」2014-3
7) 井ノ原忠彦 型技術(日刊工業新聞社)2019 Vol.32 No.12 p.036
8) 井ノ原忠彦 潤滑経済(潤滑通信社)2019 No.595 p.19
9) T. Sugihara, T. Enomoto, Precision Engineering, 49 (2017) 52-56
10) T. Sugihara, P. Singh, T. Enomoto, Procedia Manufacturing 14 (2017) 111-117
11) T. Sugihara, T. Enomoto, Precision Engineering, 33 (2009) 425-429
12) T. Sugihara, T. Enomoto, Precision Engineering, 36 (2012) 229-237
13) T. Sugihara, T. Enomoto, Precision Engineering, 37 (2013) 888-896
14) T. Sugihara, H. Tanaka, T. Enomoto, Procedia CIRP 46 (2016) 545-548
15) T. Sugihara, Y. Nishimoto, T. Enomoto, Precision Engineering, 48 (2017) 75-82
16) T. Hasegawa, T. Aizawa, T. Inohara, K. Wasa, Procedia Manufacturing 15 (2019) 1437-1444.
17)T. Aizawa, T. Hasegawa, T. Inohara, Proc. 12th AFGS (2019) 6-1 to 6-8.
18)T. Aizawa, T. Inohara, K. Wasa, micromachine (2019) 10-1 to 10-9.
19)T. Aizawa, Stainless steels, Ch. 3 (2019) 31-50, InTech Open.
20)相澤龍彦、プラストス(日本塑性加工学会会報誌)2(19)(2019)411-415.
21)相澤龍彦、自動車技術、72 (6) (2018) 35-41.
22)相澤龍彦、吉原正一郎、塑性と加工、60 (3) (2019) 53-58.
23)T. Shiratori, T. Aizawa, Y. Saito, K. Dohda, materials, MDPI 12 (2019) 1-11.
24)相澤龍彦、杉田良雄、芝浦工業大学研究報告理工学系、57(1)(2013)1-10.
25)A. Farghali, T. Aizawa, Mater. Trans. 58 (2017) 697-700.
26)A. Farghali, T. Aizawa, ISIJ-International, 58 (3) (2018) 401-407.
27)T. Aizawa, T. Yoshino, T. Shiratori, S-I. Yoshimura, ISIJ-International, 59 (10) (2019) 1886-1892.
28) T. Katoh, T. Aizawa, T. Yamaguchi, Manufacturing Review 2 (2) (2015) 1-7.