微細表面構造による切削工具の高機能化とその構造最適化
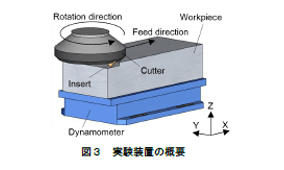
微細表面構造による切削工具の高機能化とその構造最適化
杉原達哉*1,榎本俊之*1
Development of cutting tool with textured surface and optimization of texture pattern
Tatsuya SUGIHARA, Toshiyuki ENOMOTO
Key words : Cutting, Texture, Tool wear, Tribology
1.緒 言
切削加工において工具の長寿命化は常に重要な課題であり,工具摩耗や切りくず凝着による工具折損のさらなる抑制が強く求められている.こうした要求に対し,著者らは工具表面にナノ~マイクロメータオーダの微細な三次元周期構造を形成することで様々な機能を発現する工具,すなわち微細表面構造を有する高機能切削工具の提案・開発(1), (2)を行っている.そ してこれまでに,工具すくい面に周期溝構造を付与することに よって,切削工具の耐凝着性(1)や耐摩耗性(2)といった様々な特 性が著しく向上することを明らかにしてきた.こういった工具表面の微細な三次元構造に関する研究は国内外で年々数を増やしている状況であり(3-8),工具表面構造がもたらす様々な効果が報告されている.しかしながら,それらの効果は表面構造の形状や寸法に大きな影響を受けることが知られている一方で,明確な構造設計指針は未だ明確にされておらず,現状では試行錯誤のみによって探索が行われている状況である.さらに,ピストン/シリンダーなどの摩擦摺動面においては,ディンプル状の表面構造が優れた摩擦特性を示すことが知られてい るが(9), (10),切削工具に関する研究の多くは溝状の周期構造に関する検討となっており,ディンプル構造が切削工具表面に導入された事例はほとんど無い.特に,ディンプル構造は“クローズドな構造”であるため,溝構造などの“オープンな構造”とは 異なる効果の獲得が期待できるほか,それぞれの構造に適した加工環境・加工条件が存在する可能性があると言える.
そこで,本研究では様々なディンプル構造を表面に有する切削工具を新たに開発し,鉄鋼材料の切削加工における加工特性の評価を行った.さらに,溝構造ならびにディンプル構造を有する切削工具を用い,異なる潤滑環境下での加工特性の比較を行うことで,各構造の特性の抽出を行い,適切な表面構造の選択指針の明確化を行った.
2.ディンプル構造を有する切削工具の開発
本研究では,超短パルスレーザ(リプス・ワークス製 PiCooLs4,中心波長 515 nm,パルス幅 190 fs,繰り返し周波数 400 kHz)を使用し,すくい面に微細なディンプル構造の形成を行った.図1に開発工具の概要を示す.同図に示すように,超硬合金製工具(住友電工ハードメタル製 SEKN 42MT ; A30N,チャンファ幅:100μm)のすくい面に,微細なディンプル構造を加工している.
本研究では,図2に示すように,ディンプル径(Ddia),ディンプル間隔(Din),ディンプル配列(Linear, Zigzag)をパラメータとし,DT-01からDT-10までの10種類の工具を用意した(表 1).ディンプル深さ(Ddep)は 5 μm,切れ刃先端からディンプルまでの距離(Ew)は 30 μmで統一している.また,面積比(Ar)は,各構造のすくい面上のテクスチャ凹部が占 める割合を示している.
3.ディンプル構造を有する切削工具の加工特性
3.1 ウェット加工における耐摩耗性
開発工具のウェット加工環境下における耐摩耗性を評価するため,エマルションタイプの水溶性切削油剤を使用し,一枚刃による正面フライス切削加工実験を行った(図 3).加工実験には立型マシニングセンタ(ヤマザキマザック製AJV-18) を使用した.主な実験条件を表1に示す.被削材には S53C(焼鈍し材)を使用した.加工後の工具すくい面はレーザー顕微鏡(キーエンス製 VK-X250)によって観察を行い,切削距離 300 m の時点でのクレータ摩耗量を測定した.
図4 は,各工具の工具すくい面に生じたクレータ摩耗の最大深さと,各工具の表面構造の面積比の関係を示したものである.なお,テクスチャを付与していない通常の工具については,面積比が 0 の工具として同図中にプロットしている.同図からわかるように,通常の工具では深さ約9 μm程度のクレータ摩耗が発生しているのに対し,いくつかの開発工具では大きく摩耗を抑制できていることがわかる.さらに,テクスチャ工具の耐摩耗性は面積比に大きな影響を受けており,面積比約 20%以下ではほとんど効果が得られていないのに対し,20%以上では面積比に比例して工具の耐摩耗性が向上している.また,図 4 (a)ならびに(b)を比較してわかるように,本実験条件下においては,テクスチャの配列はほとんど影響を及ぼしていないことも明らかとなった.図 5 は通常の工具,ならびに優れた耐摩耗性を示した DT-05 の工具すくい面の三次元形状および断面形状を示している.同図に示すように,切削距離300 mの時点では,DT-05のすくい面に形成したディンプル構造が明確に残存しており,DT-05 の鉄鋼材料の切削加工における優れた耐摩耗性が確認できる.
3.2 ドライ加工における耐摩耗性
開発工具のドライ加工環境下における耐摩耗性を評価するため,通常工具および開発工具を用いてドライ加工実験を行った.その他の実験条件は表 2 に示す通りである.
図 6 に,ドライ加工における各工具の工具すくい面に生じたクレータ摩耗の最大深さと,各工具の表面構造の面積比の関係を示す.ウェット加工時(図 4)と比較して,通常工具,開発工具ともにドライ加工では摩耗量が増大しているが,これはドライ加工では切削油剤の冷却・潤滑効果が得られないことから,工具-切りくず界面の熱的・機械的負荷が増大していることが原因であると言える.その一方で,ウェット加工時と比較して通常工具に生じた摩耗量との差は小さくなっているものの,いくつかの開発工具はドライ加工においても耐摩耗性が向上していることも確認できる.また,ドライ加工においてもディンプル構造の耐摩耗性は面積比に影響を受けていることが確認できる一方で,ウェット加工時(図 4)とは異なり,DT-05 と DT-09,DT-06 とDT-10 のように,面積比がほぼ等しいにも関わらず摩耗量に差が現われている工具が存在している.ここで,DT-05とDT-09 のドライ加工後の工具すくい面のSEM像を図 7 に示す.同図に示すとおり,ディンプル径の小さなDT-09 では凝着物によってディンプル構造が埋没してしまっているのに対し,DT-05 は加工後も構造が凝着物に埋没せずに残存している.以上の結果から,ドライ加工のような凝着が生じやすい加工環境下において,テクスチャ構造の面積比が等しい場合では,少量の凝着物で構造が埋没してしまうディンプル径の小さな構造より,DT-05 ならびに DT-06 のようなディンプル径の大きな構造のほうが有利であることを示してい ると言える.
3.3 摩耗抑制メカニズムの解明
工具すくい面に形成されたディンプル構造は,(1) 切削油剤を工具-切りくず界面に保持する Micro pool としての効果,(2) 硬質な摩耗粒子をトラップする Micro pocket としての 効果などを得ることによって,優れた耐摩耗性を発現していると考えられる.そこで,これらの効果の影響を個別に評価するため,ウェット加工,ならびにドライ加工における工具-切りくず間の摩擦係数の評価を行った.本実験では,図 3 に示すように被削材下部に設置した三分力動力計(Kistler 製 9257B)によって切削抵抗の測定を行い,工具すくい面に対して鉛直方向成分と平行方向成分の比を求めることで,摩擦係数を導出した.
図 8 に,通常工具,ならびに DT-05 のウェット加工時,ドライ加工時のそれぞれの摩擦係数を示す.同図に示すように,切削液が供給されないドライ加工環境下においても,開発工具の摩擦係数が通常の工具と比較して低減していることがわかる.ここで,(2) 硬質な摩耗粒子をトラップする Micro pocket としての効果については乾燥状態においても発現することから(11),この結果は開発工具で同効果が得られていることを示していると言える.また,図 6 に示したドライ加工環境下における開発工具の優れた耐摩耗性についても,この効果の影響が大きいと考えられる.その一方で,開発工具のドライ加工時とウェット加工時の摩擦係数を比較すると,その差は通常工具のドライ加工とウェット加工の差よりも大きい.したがって,開発工具のウェット加工時には,微細表面構造が Micro pocket としての効果だけでなく,(1) 切削油剤を工具-切りくず界面に保持する Micro pool としての効果 を発現することで,工具-切りくず間の潤滑性が高まったと考えられる.以上の結果から,ディンプル構造を有する切削工具は,(1) 切削油剤を工具-切りくず界面に保持する Micro pool としての効果,(2) 硬質な摩耗粒子をトラップする Micro pocket としての効果の双方を発現することによって,優れた耐摩耗性を示していると言える.
4.最適構造の明確化
上述のディンプル構造は,個々の構造が閉じた“クローズドな構造”をしているのに対し,溝構造などは繋がった一連の構造で構成される“オープンな構造”であると言える.こういった違いは,切削油剤の保持性/流入性の違いや方向依存性の有無,切りくず流出性に対して大きな影響をもたらすことが予想される.そこで,本研究ではディンプル構造を有する切削工具,ならびに周期溝構造を有する切削工具の加工特性をそれぞれ比較し,特徴の抽出を試みた.
4.1 周期溝構造を有する切削工具の加工特性
先行研究(2)では,工具すくい面に微細な周期溝構造を有する切削工具を開発し,同工具が鉄鋼材料の切削加工にお いて優れた耐摩耗性を示すことを明らかにしている.そこで,本研究ではまず,溝幅・溝間隔 20 μm,溝深さ 5 μm の一方向からなるストライプ状の周期溝構造を有する切削工具(MS-01)を用いて表 2 の条件下で加工実験を行い,その耐摩耗性を評価した.なお,周期溝構造の耐摩耗性は,寸法や方向に大きな影響を受けることが明らかとなっているが,MS-01 は先行研究において最も優れた耐摩耗性を示した工具の一つである.
図 9 は,切削距離 300 m(ウェット加工)の時点における MS-01 の工具すくい面の三次元形状,ならびに断面形状である.同図に示すように,周期溝構造を有する切削工具は,通常の工具と比較して大きくクレータ摩耗を抑制できており,ディンプル構造(図 5)とほぼ同程度の摩耗量(深さ約 3 μm)となっている.また,ディンプル構造と同じく,切削距離 300 m の時点では溝構造が明確に残存しており,周期溝構造を有する切削工具の優れた耐摩耗性が確認できる.
4.2 異なる潤滑環境下における加工特性の比較
オープンな構造,クローズドな構造の特性をより詳細に抽出するため,ウェット加工,ドライ加工,ペースト加工の異なる三種類の潤滑環境下における摩擦係数の比較を行った.ペースト加工については,回転工具が侵入する側の被削材側面にペースト状の潤滑剤を塗布して加工を行っているため,工具 1 回転毎に工具-切りくず界面に微量の潤滑成分が供給されることとなる.したがって,ウェット加工<ペースト加工<ドライ加工の順に,より 過酷な潤滑環境下での加工となる.
図 10 は,通常の切削工具,ディンプル構造を有する切削工具(DT-05),周期溝構造を有する切削工具(MS-01)のそれぞれの潤滑環境下における摩擦係数を示している.ウェット加工時の摩擦係数を比較した場合,わずかながらではあるものの,MS-01 が最も小さな摩擦係数を示している.これは,十分な量の切削油剤を供給して加工を行うウェット加工環境下においては,切削油剤の流入性に優れる“オープンな構造”である周期溝構造は,構造を介して工具-切りくず界面への加工中の切削油剤の供給が可能であることが要因であると考えられる.その一方で,ペースト加工時の摩擦係数を比較すると,MS-01 はドライ加工時とほとんど同程度の摩擦係数となっているのに対し,DT-05 はドライ加工時より小さな摩擦係数を示している.これは,ペースト加工では工具が被削材に接触している間の潤滑成分の供給が無いため,“オープンな構造”である周期溝構造は一度供給された潤滑成分が溝の端部からリークしてしまう恐れがあるのに対し,“クローズドな構造”であるディンプル構造は潤滑成分の保持性に優れるため,より優れた摩擦特性を示したと 考えられる.
以上の結果から,潤沢な切削油剤の供給が可能な場合は“オープンな構造”が,MQL 加工など油剤供給量が限られる場合では“クローズドな構造”が有効である可能性が示されたといえる.
5.結 言
本研究では,微細表面構造の導入によって切削工具の高機能化を図り,構造最適化の指針を明確化することを目的に,ディンプル構造を表面に有する切削工具の開発を行った.そして,開発工具の鉄鋼材料切削における加工特性を評価した結果,ディンプル構造が優れた耐クレータ摩耗性を示すことを明らかにした.
さらに,様々な加工環境下において,周期溝構造を有する切削工具との比較を行うことによって,潤沢に切削油剤が供給される環境下では溝構造などの“オープンな構造”が有利に働く一方で,油剤供給量が限られる環境下ではディンプル構造などの“クローズドな構造”が有利となる可能性が示された.
6.謝辞
本研究の遂行にあたり多大なご協力を賜りました,株式会社リプス・ワークスに深く感謝いたします.
7.参考文献
1) T. Sugihara, T. Enomoto, Prec. Eng., 36, 2 (2012) 229-237.
2) T. Sugihara, T. Enomoto, Prec. Eng., 37, 4 (2013) 888-896.
3) N. Kawasegi, H. Sugimori, H. Morimoto, N. Morita, I. Hori, Prec. Eng., 33, 4 (2009) 248-254.
4) T. Obikawa, A. Kamio, H. Takaoka, A. Osada, Int. J. Mach. Tool Manufact., 51 (2011) 966-972.
5) P. Koshy, J. Tovey, Ann. CIRP, 60, 1 (2011) 153-156.
6) A. Fatima, P.T. Mativenga, Int. J. Adv. Manuf. Technol., 69 (2013) 771-776.
7) J. Xie, M.J. Luo, K.K. Wu, L.F. Yang, D.H. Li, Int. J. Mach. Tool Manufact., 73 (2013) 25-36.
8) D.M. Kim, I. Lee, S.K. Kim, B.H. Kim, H.W. Park, J. Mater. Process. Tech., 229 (2016) 160-171.
9) I. Etsion, Tribol. Lett., 17, 4 (2004) 733-737.
10) M. Wakuda, Y. Yamauchi, S. Kanzaki, Y. Yasuda, Wear, 254 (2003) 356-363.
11) N. P. Suh, H. C. Sin, , Wear, 69, 1 (1981) 91-114.