ピコ秒レーザによる多次元微細パターン加工技術の開発
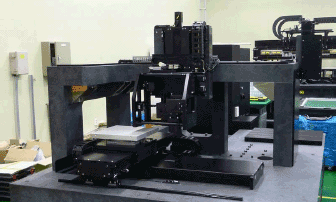
平成22年度戦略的基盤技術高度化支援事業
ピコ秒レーザによる多次元微細パターン加工技術の開発
研究開発成果等報告書
平成23年9月
委託者 関東経済産業局
委託先 財団法人理工学振興会
目次
1. 研究の概要
1-1. 研究開発の背景・研究目的および目標
1-1-1. 研究開発の背景
1-1-2. 研究の目的および目標
1-2. 研究体制
1-2-1. 研究組織
1-2-2. 管理体制
1-2-3. 研究者氏名
1-2-4. 協力者
1-3. 成果概要
1-4. 当該研究開発の連絡窓口
2.研究内容および成果
2-1. ピコ秒レーザー加工環境とレーザー制御機能の高度化
2-1-1. ピコ秒レーザー位置制御技術の開発
2-1-2. ピコ秒レーザー加工環境清浄化技術の開発
2-1-3. ピコ秒レーザー加工手順の最適化
2-2. 高制御ピコ秒レーザーによる1次元パターン加工
2-2-1. 1次元加工における形状不整(ダレ)解決加工技術の開発
2-2-2. 1次元加工の高精度化技術の開発
2-2-3. 1次元加工の高速化と2次元穴配置の高再現性の確立
2-3. 高制御ピコ秒レーザーによる多次元パターン加工
2-3-1. 多軸光学制御装置の開発と高制御ピコ秒レーザーによる2次元パターン加工
2-3-2. 高制御ピコ秒レーザーによる3次元パターン加工
2-3-3. 多次元パターン化した型技術の提案
3. 全体総括
3-1. 研究開発の成果および課題
3-1-1. 研究開発の成果
3-1-2. 今後の課題
3-2. 事業化展開
4. 専門用語等の解説
1.研究開発の概要
1-1.研究開発の背景・研究目的および目標
1-1-1.研究開発の背景
情報家電機器の高度化に伴い、特に電子制御系を内蔵した部品、パーツが増加しつつある。また、高解像度デジタルカメラ、携帯用カメラあるいは測定・分析機器の分野においても、種々の光学素子の高精度化が要請されており、例えば、DOE※1)(Diffractive Optical Element)のように、光学設計した微細パターンを転写できる金型(マザーツール)が必要となる。これらに対応するためには、以下に示す①から③のレーザー微細加工技術の確立が必須である。
①微細ピンホール加工、高アスペクト比※2)(穴径に比較して深い貫通穴)穴加工などの1次元加工(⇒レーザー入射側の形状不整と回転切断面の入射側形状不整の解決)
②電子回路の直接加工描画、周期溝パターン、周期穴パターンなどの2次元加工(⇒多数穴の高精度・高速加工技術の確立)
③ フレネルパターンなどの回折格子パターン、DOEなどの3次元加工(⇒底面の高精度平坦度不整の解決、多次元パターン加工技術の検証)
これらの微細加工は、これまでの機械加工や化学的処理では対応できず、レーザー加工での対応が期待されている。例えば、半導体検査に使用されるプローブカード※3)用基板は、マシナブルセラミックス※4)に機械加工で、プローブと呼ばれる探針を固定する穴(Ø40µm~Ø100µm)を数千穴/枚加工してきた。しかし、最新のバーインテスト※5)での高温化(125℃~150℃)に伴い、シリコンに膨張係数を近づけた高硬度材(ファインセラミックス)に、より微細な穴(Ø30µm~)を数千個レーザーで加工する必要性が複数の半導体検査用プローブカードメーカーから寄せられている。又、同様に小径(Ø60µm~Ø140µm)の金属パイプにスプリング機能を持たせたプローブピン※6)の要求も高まっている。
また、相澤らも特願2009-094693「光学素子用成形型及びその製造方法」の中で、光学素子のマザーツール作成には、上述の①から③の技術要素が必須不可欠な技術であると述べている。
ところで、レーザー技術は、レーザーが発振に成功してから50年余になる。この間、多くのレーザー媒質の発見、波長変換技術・短パルス化技術の発展により、現在は、高出力・高速化・高精度化が特徴となっており、当初の熱加工の代替技術から、微細加工(超微細加工)を含めたマイクロ加工の時代に突入している。微細加工には、極薄板の切断や溶接、ミクロンオーダーの微小な穴あけ加工や溝加工などがあり、微細加工用レーザーとして、短波長レーザーや短パルスレーザーが多く世に出ている。例えば、前者では、YAG第3高調波、後者では、従来のナノ秒レーザーに加え、ピコ秒レーザー※7)、フェムト秒レーザーが発表されている。しかしながら、YAG第3高調波では、熱影響が大きく、高アスペクトの穴あけ加工は困難であることに加え、材料によっては加工不能となるなど技術的課題も多い。熱影響を避けるためには、加工時間が十数秒かかり経済性に問題が残っている。また、ピコ秒レーザー、フェムト秒レーザーの発表事例は、生産レベルの精度と加工特性を実証できる産業界向け量産化技術には未だ達していない。
株式会社リプス・ワークスは、レーザー加工会社として、エキシマレーザー加工機(パルス幅30ns)、THG-YAGレーザー加工機(同30-70ns)、Tea-CO2レーザー加工機(同1μs)およびファイバーレーザー加工機(5μs)を駆使し、主に微細加工技術を蓄積してきている。
斯かる実績からプローブカードメーカー、その材料メーカーおよびプローブピンメーカーなどから、基板の高温化に伴い硬度材(ファインセラミックス)に微細な穴(Ø30µm~)を数千個加工する可能性について打診を受けているが、これまでのレーザーでは、熱影響によるデブリ※8)やダレが生じ、要望仕様とは大きな乖離があることが分かった。そこで、原理的にみて技術確立の可能性の高いピコ秒レーザー加工機(パルス幅8~10ps)を選択し、独自の光学系・制御系を整備し、予備的検討をしてきた。その結果、ピコ秒レーザーを高精度で制御することで、ダレがなく、しかも要求される高いアスペクト比で穴加工できる可能性が見出されてきた。同様にプローブピンにスプリング機能を持たせる技術についても、パイプ状の金属に精度良く、らせん状に切れ目を施す可能性が見出されてきた。
1-1-2.研究の目的および目標
本研究開発の目的は、ピコ秒レーザーによる高硬度材への微細穴あけ技術に関する株式会社リプス・ワークスの自主研究の成果を踏まえ、高速かつ高精度の穴あけ加工技術を確立することである。さらに、他の材料への微細穴あけ技術(1次元加工)、多数穴を高精度ピッチで加工する技術(2次元加工)、微細金型への応用(3次元加工)など、より特性の優れた多次元微細パターン加工技術の開発を行う。この技術の確立により、機械加工、放電加工、既存レーザー加工に比べ高速・高精度の微細加工を実現することができ、半導体、半導体検査機器、自動車、医療機器、光学素子などの業界の将来ニーズに対応可能となる。
研究の目標として、まず、高硬度材への高速かつ高精度の微細穴あけ加工技術(1次元加工)を確立する。その目標値を、高純度アルミナ、窒化アルミ、窒化珪素、マシナブルセラミックスの加工で、真円度1µm・アスペクト比10・加工速度5秒/穴以内とする。
1-2.研究体制
1-2-1.研究組織
1-2-2.管理体制
1-2-3.研究者氏名
1-2-4.協力者
なし
1-3.成果概要
株式会社リプス・ワークスの自主研究の成果と独立行政法人産業技術総合研究所のレーザー加工技術及び芝浦工業大学の光学系素子・表面処理技術とを融合して、レーザービーム光学系の整備、特に高速回転する光学系の高信頼性を確保するため高剛性に留意して、ピコ秒レーザー位置制御装置を開発し、ピコ秒レーザービームによる多次元加工の制御が可能となった。また、製品精度に影響を与える温度変化を最小限に抑え、微塵、微粉などを含む汚染因子を清浄化するピコ秒レーザー加工環境清浄化装置を開発し、技術確立環境を整備した。1次元加工では、ビーム特性の調整、位置制御との同期などをチェックし、形状不整を無くし、高真円度・高アスペクト比の穴加工の実現と高精度回転制御装置を開発し、平滑な回転切断の技術を確立した。
また、ピコ秒レーザー位置制御装置の速度と空間分解能をパラメーターに周期的な穴構造の高速1次元加工の可能性を探索し、そのための制御条件を調査した。特に被加工材による加工速度の相違と加工速度限界を決める要因について考察し、多穴加工部品の量産化のための高再現性を実証した。
2次元加工・3次元加工では、底面の平滑度の加工技術を確立するためにレーザーの焦点位置と材料の高さ位置を高精度に調整する多軸光学制御装置を開発し、周期パターンにおけるピッチ精度・形状急峻度・面粗さ精度・底面の平坦度などに留意し、最適加工条件の探索とパターン再現限界の検討を行い、微細パターン分析装置によりその精度を評価した。さらに、シリコン、シリコンカーバイド型およびDLCコーテッド工具鋼型を作製し、本技術の有用性と光学素子生産用の新しいマザーツール創製法(型技術)としての可能性を探索した。
加えて、開発する微細パターン転写モールド成型装置により、光学ポリマーならびに低融点ガラスを素材として利用し、2次元ならびに3次元パターン加工した型を用いて、そのモールド成形転写性を検討した。
1-4.当該研究開発の連絡窓口
財団法人理工学振興会 事務局長 泉洋一郎
TEL:045-921-4391/FAX:045-921-4395
2.研究内容および成果
2-1.ピコ秒レーザー加工環境とレーザー制御機能の高度化
2-1-1.ピコ秒レーザー位置制御技術の開発
(1)ピコ秒レーザー位置制御装置
本研究用に開発したピコ秒レーザー位置制御技術を搭載した加工機について説明する。
ピコ秒レーザーを用いた加工では、数ミクロンの位置制御精度、姿勢制御を求められることから、加工機本体は高剛性であると共に、温度変化に対する安定性や加工機外から伝達される振動や加工機に搭載する駆動部から発生する振動に対して、振動減衰能が高いなどの特性を有する素材で構築する必要性がある。
また、発振器出口から放射されるレーザービームが加工点に至る過程でポイントスタビリティ(位置安定性)が外的要因(振動等)により害されない構造でなければならない。
そこで、本研究用に開発した加工機には高剛性、振動に対する高減衰能、温度に対する安定性の全ての面で高い性能を有するグラナイト材を構造部材として用いた。振動に対しては、 アジャスタ部にパッシブ型の除振パッドを使用し、外部からの振動の伝達を防ぐ構造とした。写真2.1は、開発した加工機の構造写真を示す。
本研究開発で用いたグラナイト材の物理特性を、加工機のベース材として多く用いられる鋳鉄と比較して表2.1に示す。鋳鉄は、木型の設計形状に合わせて自由な形状に製作でき、素材中に分散する黒鉛の効果により振動減衰能が高く、工作機械のベース材として多く用いられる。大型の鋳物は、内部応力による経年変化を取るために、鋳造後に長期間放置し、熱処理する必要がある。一方、グラナイト材は、形状の自由度は限られるものの、鋳鉄に比べヤング率、比強度(重量あたりの強度)が高く剛性を得やすい。線膨張率、熱伝導率が小さく、鋳物より振動減衰能が高い等、高精度な加工機のベース材として必要な特性を持っている。
(2)レーザー発振器
搭載するレーザー発振器は、ドイツTRUMPF社製高出力ピコ秒レーザー発振器である。
(3)レーザー伝送光路
グラナイトベースの上にレーザー発振器を搭載し、他の光学部品と共に光路を形成した。
(4)レーザービームローテーター
自主開発したレーザービームローテーターを搭載した。
(5)X-Y、θステージの精度
ピコ秒レーザー位置制御装置に搭載したX-Yステージはリニアモータ駆動方式のステージを使用した。ガラススケールの目盛りをフィードバック制御しながら位置決めし、高精度な位置決めを実現する。また、θ軸はワークの回転補正をするためのもので、ワーク上のアライメントマークを高倍率(×500)カメラで撮像し、回転方向の位置補正ができる機構である。表2.2、図2.1に製作したX-Yステージの特性をまとめる。
2-1-2.ピコ秒レーザー加工環境清浄化技術の開発
高精度なピコ秒レーザー加工を効率的かつ高信頼度で行うために、加工条件及び製品精度に影響を与える微塵・微粉などを含む汚染因子を清浄化するピコ秒レーザー加工環境清浄化装置を製作した。加工室には23~28℃で安定できる空調機を設置し、直射日光が加工装置の一部であっても当たることのないように窓を遮蔽物で覆い、加工装置を窓部から遠ざけてレイアウトした。
加工室全体の温度を安定させ、その安定した雰囲気をそのまま加工機内に導入することで、加工室内外の温度差をなくし、加工機への影響のみならず、ワークの温度の安定化も同時に計れるようにした。加工装置内部へ温調された空気の導入は、HEPAフィルター付きファンユニットを天井部に配置することで実現した。
筐体は、全て金属性でレーザー光が外部に漏れ出ないようにした。写真2.2は、ピコ秒レーザー加工環境清浄化装置をピコ秒レーザー位置制御装置に取付けた写真である。
また、図2.2にピコ秒レーザー加工環境清浄化装置を取付けた内部温度の経時変化を測定したデータをまとめる。外気温度の変動で大きなうねりはあるものの、昼夜問わず、±2℃以内に入っている。写真2.3は温度測定位置を示す。(写真は測定位置が判りやすいように加工機本体の写真に位置を示すが、実際はピコ秒レーザー加工環境清浄化装置内で測定。)
2-1-3.ピコ秒レーザー加工手順の最適化
ピコ秒レーザーの加工をより効率化するため、各種加工光学系をZ軸に搭載し、加工対象に応じて、加工光学系を自動で交換できる機構を設けた。写真2.4は、加工光学系搭載部の外観である。
2-2.高制御ピコ秒レーザーによる1次元パターン加工
2-2-1.1次元加工における形状不整(ダレ)解決加工技術の開発
高アスペクトの微細穴を多数、形状不整を無くし高精度で加工するために、収差等を含むビーム整形光学系(集光光学系)の整備・調整を行う。さらに、回転切断面の平滑度確保のためにレーザーと同期した高精度回転制御装置を開発する。
(1)無収差光学系
今回の研究には、無収差光学部品としてグラディウムレンズを使用した。
(2)高精度回転制御装置
パイプ状のワークに螺旋形状の加工を行なう場合、低速でも高度な送りと回転制御が可能な高精度回転制御装置が必要となる。本研究では、当社の要求を満足する2軸回転制御装置を選択した。
(3)形状不整の原因となるビーム非点収差の改善
レーザー加工部の形状不整には次の二つの現象がある。一つは、穴形状が楕円になる。もうひとつは、レーザー入射側のダレである。
本項では、これらの不整に対し、改善を試みたので、説明する。
①楕円穴の検討
レーザービームをビームローテータで回転しているので、レーザービームが真円であれば、その形状で加工ができるが、ビーム形状が真円でなければ、その形状を拡大してしまう。
このことから、加工点でのレーザービームの状態を観察してみた。焦点位置を変えながら、レーザーを照射し、その加工痕の形状を調べてみると、ジャストフォーカスの位置を挟んで上下位置で加工痕の形状がX方向とY方向に変化することが判った。これは非点収差と呼ばれる現象で、レーザービームの持つP波とS波の焦点位置が異なるために起こる現象で、レーザー発振器が持つ固有の特性に伝送光学系部品の品質によるものと考えた。
そこで、伝送光学系に使用するミラーにおいて、その面精度を向上させることで対策を図ってみた。写真2.5は高純度アルミナにおけるその改善事例である。
②ダレの改善検討
レーザービーム入射側に発生するダレの発生は、完成品の性能への影響もあるが、寸法測定において、誤差を生む要因となり、ダレを無くする=測定精度の向上にも繋がる。
ダレの要因としては、前述のレンズの違いによる集光性能の影響や、非点収差の影響などが複合的に作用していると考えられる。また、レーザー出力条件や焦点位置の影響もあり、容易に解決することはできない。そこで加工方法の工夫により解決した事例を写真2.6に示す。
写真2.7は無収差光学系のみの螺旋形状加工の改善例である。
また、当該研究分野における関係する学術文献の検索調査を行い、レーザー深穴加工における課題や重要ポイントを調べた。ビーム回転制御装置を用いた検討例として下記論文が報告されており、1mm厚程度の窒化アルミ基板に100から400ミクロン径の深穴加工がTrepanning方式の利用でテーパー角がほぼ90°の加工が達成されている。しかしながら、レーザー入射側穴や出射側穴表面はやや荒れて損傷していることが文献内の図8に示されている。
題目:Advanced Laser Micro Machining Using a Novel Trepanning System
著者:David ASHKENASI, Norbert MUELLER, Tristan KASZEMEIKAT, Gerd ILLING
所属:Laser- und Medizin-Technologie Berlin GmbH (LMTB), Berlin, Germany
雑誌名:JLMN-Journal of Laser Micro/Nanoengineering Vol. 6, No. 1, p.1(2011)
また、回転制御機構を有しない照射系での深穴加工時に発生する穴方向の偏向状態を非破壊方法で測定した報告2件があった。0.5mm厚のシリコン基板を1030nm光で加工し、1060nm光で側面方向から観測している。8psのパルス幅の加工光源を用いているが、ビーム回転制御装置を有しないために、約1000パルス照射を超えたところから加工穴内部側面に偏向した加工痕が発生していることが示されている。
題目:In situ imaging of hole shape evolution in ultrashort pulse laser drilling
著者:Sven Döring, Sören Richter, Stefan Nolte, and Andreas Tünnermann
所属:Institute of Applied Physics, Friedrich-Schiller-University, Jena, Germany
Fraunhofer Institute of Applied Optics and Precision Engineering, Jena, Germany
雑誌名:OPTICS EXPRESS Vol. 18, No. 19, P.20395 (2010)
題目:In-situ observation of the hole formation during deep drilling with
ultrashort laser pulses
著者:Sven Döring, Sören Richter, Stefan Nolte, Andreas Tünnermann
所属:Institute of Applied Physics, Friedrich-Schiller-University, Jena, Germany
Fraunhofer Institute of Applied Optics and Precision Engineering, Jena, Germany
雑誌名:Proc. of SPIE Vol. 7925 792517-1(2011)
2-2-2. 1次元加工の高精度化技術の開発
無収差光学系の採用と伝送光学系の改善により非点収差が改善され、加工面でのレーザービーム形状を改善したことと、ピコ秒レーザー位置制御装置の剛性が大きく寄与し、研究の目標であった下記の数値は達成できている。ただし、下記の目標値を達成するために要した時間は12秒/穴であった。時間的な目標値は5秒/穴である。加工時間を5秒/穴にすると真円度が±1µmになる。現状での顧客の要求精度は±1μmでも可であるため時間短縮と加工精度の関連は今後の課題とする。
表2.3に目標値と達成値を示す。
また、1次元加工の深穴内部の状態を観察するにあたって、非破壊でその加工品位を調べる方策として1次元加工物のレプリカ作製手法を候補として選び、その適用可否を検討した。レプリカ材料としてストルアス社製レプリセット(型番:T3)を選択した。これは、シリコン樹脂を主成分とする熱硬化性エラストマ材料であるが、純シリコン樹脂よりも柔軟性やコシの強さに優れており本用途に適した材料であると判断した。また、レプリカ作製時の対向側の保持基板として平行平面基板およびウエッジ基板を採用し、レプリカ作製用治具を組み立てた。保持基板には主として平行平面基板を用いた。用途に応じて角型基板(20mm角)および丸型基板(20mm径)を使用した。特殊事例としてウェッジ基板を用いて剥離性能を検討したが、平行平面基板と差異は見られなかった。また、治具は加工基板を保持した状態で、鉛直方向に微動する機構を有しており、高アスペクト比1次元深穴構造物のレプリカを取得する際にレプリカ物の破断を極力回避することを意図した動作を行うことができる。治具の個別部品はレーザー加工に使用する際の汎用消耗部品を使用し、それらを適時組み合わせて治具を構成させた。
検討初期段階でのレプリカ構造物のSEM写真を写真2.9に示す。深穴からのレプリカ構造物を回収できたのはごくわずかで(左写真9番と右写真8番のみ)、大半は根元から破断しており、歩留まりの悪い状態であった。そこで、剥離方向や速度ならびに樹脂硬化時間を最適化する検討を鋭意実施し、現在のところ、写真2.10に示すところまでに作製技術を向上させることができた。3つの構造物を1組として、照射時間を11種類変えて深穴加工を列状に行った試料で、右側から徐々に照射時間が増えて、深穴が形成されていることを明瞭に捉えることができた。左端構造物の拡大写真においても、突起物の側壁面の微細な凹凸構造を捕捉していることがわかる。これらの結果から、50ミクロン径の深穴構造物に対して、良好なレプリカ構造体を作製する手法を確立できた。しかしながら現時点の問題点としては高い形状のレプリカ構造物は倒れやすい傾向があり(写真2.11)、不倒化の完全解決策の解明は、今後の検討課題である。
2-2-3.1次元加工の高速化と2次元穴配置の高再現性の確立
(1) ピコ秒レーザー位置制御装置の加工速度と空間分解能をパラメータとし、高速1次元加工の可能性を探索し周期的な穴構造を形成しそのための制御条件を検討する。
図2.3はそれぞれの材料にØ0.05mmの1次元加工時のレーザー出力と加工時間の関係を示す。
(2)2次元穴配置の高再現性の確立
顧客からサンプル指定されたマシナブルセラミックス(t=0.25mm)にØ0.035mmの周期的穴構造をニコン製NEXIVにて測定した結果を図2.4に、図2.5に加工の時系列的寸法変化を示す。また、表2.4に1次元加工の高速化と2次元穴配置の高再現性確立の目標と達成値を示した。
2.3.高制御ピコ秒レーザーによる多次元パターン加工
ここでは、2.1,2.2で開発した、高精度位置制御機能、ローターによるレーザービーム制御機能などを備えたピコ秒レーザー加工装置を用い、DLCコーティング、グラッシー・カーボン材(以下GC材)および炭化ケイ素材(以下SiC材)への多次元パターン形成を行い、その形状寸法評価を行った。さらに、開発した真空モールド成形装置を用いて、パターン形成した型材からの光学プラスチック材へのパターン転写成形実験を行い、製品へのパターン転写性能についても実験的に調査した。
2-3-1.多軸光学制御装置の開発と高制御ピコ秒レーザーによる2次元パターン加工
(1)多軸光学制御装置の開発(本事業)
ピコ秒レーザー位置制御装置は、X,Y,Z,θ軸を搭載し、また、前項で説明した高精度回転制御装置を着脱して使用することができる。しかしながら、2次元ならびに3次元の微細パターンを実現するためには、これらの駆動軸以外に、ワークを上下して加工できる軸が必要となる。そのため、AEROTECH社の上下動を高度に制御できるZ軸をワークを上下させる軸(写真2.12)として採用した。これにより、ピコ秒レーザー位置制御装置が持つ光軸を上下させるだけでは困難な、高度な3次元加工が可能となる。図2.6は、その概念図を示す。
片側の面を垂直に加工するなど非対称な3次元加工には必要となる。
次に、高制御ピコ秒レーザーを用いて、マイクロV字グルーブ加工を行い、その形状寸法特性を評価した。特にアスペクト比に留意し、そのレーザー加工特性について調査した。また高精度表面形状測定も行い、目標とした2次元パターンに対する形状制御性についても考察した。
(2)加工素材
多次元パターン形成用の素材として、写真2.13に示すグラッシーカーボン素材(GC材)を共通に用いた。当該素材は、きわめて脆性で切削加工による機械的除去加工では全く加工は不可能である。しかし、高温までの強度はすぐれており、本多次元パターン形成の目標の1つである炭素系素材へのパターン形成には最も適した素材である。
次に加工用素材として用いたのが、炭化ケイ素素材(SiC材)である。写真2.14に示すように、モールドプレス用型形状に焼結できることに加え、コーティングとしての素材形成およびDLC-SiCの複合コーティングとしての素材形成も可能なため、多次元パターン形成用素材として広く応用できる。さらに電気伝導度も制御することも可能であり、今後ほかのパターン形成法との比較および形成パターンと電気伝導性異方制御の関連などの調査にも利用できる。
第3の多次元パターン形成用素材は、DLCコーテッド型材である。現在、PVDおよびCVD法を用いて、10-20μm厚のDLCコーティングが可能である。ほとんどすべての基材上にDLCコーティングできることから、この素材へのパターン形成ができれば、セラミックス素材に限らずポリマー材、金属素材などへの多次元パターン形成が可能となる。本実験で使用するDLCコーテッド型材を写真2.15に示す。
以下の加工実験では、GC材を中心にレーザー加工による多次元マイクロパターン形成実験を行った。転写成形実験では、DLCコーテッド型材も利用し、転写成形時の形状再現性について検討を行った。
(3)GC材を用いた2次元マイクロパターン形成
2次元パターンでは、個々の形成パターンの形状寸法を担保すると同時に、パターン間のピッチ寸法精度保証が課題となる。この実験では、マイクロV字グルーブを1つのパターンとして、その2次元パターン形成実験を、GC材を用いて行った。
レーザー加工条件として、パワー投入比率0.5%の場合に得られたV字グループパターン形成したGC材の外観と光学顕微鏡像をそれぞれ写真2.16、2.17に示す。
目標深さ加工値が10µmの加工GCサンプルである。
写真2.16中の周辺よりもやや黒く見えている部位がレーザー加工面である。1枚のGC材へのV字マイクロパターン形成にかかる処理時間は40分であり、他のパターン形成法(エッチングなど)と比較するときわめて短時間となっている。
より詳細なマイクロパターン形状を測定するため、三鷹光機製・レーザープロファイル計を用いた。図2.7に示すように、設計した20µmピッチ精度は高く、またV字形状は、10µm切削に対して、最大で+2µm、最小で-1µmの範囲で加工できている。後述するように、詳細なパターン形状はレーザー反射法による本測定では保証できないが、加工精度に関しては検討できる。
(4)2次元マイクロパターン形成におけるアスペクト比の影響
V字パターン転写実験では、目標加工深さをパラメータにして、アスペクト比の影響を調査した。一般に、一定のパワー投入比率でレーザー加工すると、アスペクト比が増大するにつれ、加工能は減衰する。ここでは、目標深さと実測深さとの対応を調べ、2次元パターンレーザー加工能を検討した。図2.7に示したパターンの1ユニットの詳細計測結果を図2.8に示す。
レーザー反射法の測定ゆえに、V字斜面の精度は原理的に保証されないが、底面位置は正確であり、この結果からも目標深さ10µmに対して、測定結果も10µmであることがわかる。底面位置に関して、加工深さ分布が非対称であるのは、レーザー光の集光形状が円ではなく楕円形状など方向性をもつことによると考えている。この測定深さと加工設定深さとの対応を調べ、図2.9で比較する。パワー投入比率が一定のままでは、到達深さが減少することが、改めて確認された。
(5)レーザ-による2次元マイクロパターン形成技術課題
2次元マイクロパターン形成では、実験で示したように、X-Yテーブル、ローター制御などによりパターン形成の制御系は完備し、マイクログルーブに限定されずに、種々のパターンデザインが可能となった。一方で、現行におけるエッチングによるパターン形成と比較すると、2つの技術要件が大きな課題となる。
第1は、パターンユニットの形状寸法とその精度であり、現行の7psでは、10µmが1つの限界である。したがって、レーザー波長を限定すれば、V字マイクログルーブで見られたように、深さ方向における高精度のパターンユニット形成が重要となる。後述するように、深さ方向の加工精度は、レーザーパワーに加え、焦点領域の形状・レーザー間の干渉など種々の要因が影響されるため、最適プロセス化に向けた研究開発が必要である。
第2は、平面パターンに対するアスペクト比の向上である。後述の3次元パターン形成でも指摘するように、光学設計上、パターンユニットとしてアスペクト比が1.0を超える形状パターンが多い。特に角錐形状などは3.0を越えるアスペクト比のマイクロパターンも重要となる。第1の技術課題とともに、パターンユニット形状に応じた高アスペクト化も重要な課題となる。
上記の課題はあるが、GC材、DLCコーテッド材あるいはSiC材など、エッチング法ではパターン形成が困難な素材に対してマイクロパターン形成できる長所が有意義で、今後の研究開発が期待される。
2-3-2.高制御ピコ秒レーザーによる3次元マイクロパターン加工
型材への3次元パターン形成は、これまでのナノ・マシニングによる微細機械除去加工でも作成が困難な形状を対象とする。この3次元パターン形成で最初に問題となるのが、急峻な面と隣接面角度保持が求められるパターン形成となる。ここでは、代表的な3次元マイクロパターンデザインを示し、そこでの技術課題を分析する。その上で、隣接面を4面含む4角錐の3次元マイクロパターン形成実験を行い、そのパターン位置精度について検討する。
(1)3次元マイクロパターンデザイン
次世代の3次元ディスプレイ用の3次元光学ガラスでは、図2.10に示すような、3次元マイクロパターンを必要とする。パターンの底面は、光学ガラスがモールドプレス成形時に最後に充満する部位であり、精度の確保のためには、成形後の研磨などにより仕上げ加工が入る部分となる。したがって、転写成形時に重要となるのは、表面から垂直にたつ側面2つならびに表面に対して16°の角度で立つ2つの側面精度である。側面の表面粗さ精度もさることながら、光学的なデザインでは、前者の垂直面のおける急峻度(表面からの角度が90°にどの程度漸近できるか)、後者の傾斜面の急峻度(16度保持)ならびに隣接面の面交線の再現精度である。実際、エッチング法などによる従来加工法では、型材が限定されることによる耐久性の低さ以上に、急峻度の喪失・隣接面交線のダレが大きな課題となっている。
当該レーザー加工においても、この急峻度と隣接面角度保持の仕様のクリアが大きな課題となるため、以下では、図2.10中に含まれる4角錐パターンユニットに注目し、その3次元マイクロパターン形成実験を行った。
(2)レーザ-による3次元マイクロパターン形成
目標形状を、一辺が50µm、深さが100µmの4角錐をユニットとし、加工ピッチを100µmで10×10の3次元マイクロパターンを、GC材上に形成した。加工面の全体像を写真2.18に示す。
加工後の4角錐パターンの入り口径は50-51µm、深さは78-80µmである。平均寸法に関しては、一定の精度が得られている。またピッチ寸法に関しても高精度位置制御ができている。
アスペクト比を大きくすると、パワーを2.5%一定で加工を行った場合、深部での加工性が低下し、すでに2次元マイクロパターン形成でも明確となったように、デザイン深さよりも実測深さが低下する。
作成した4角錐パターンの詳細を、写真2.19で調査すると、入口でダレは、4辺形の角度で顕著となり、4角錐ユニットを構成する隣接面間の角度保持が、難しいことがわかる。
ここで採用したレーザー加工パス方法は、図2.11のように、ガルバノを用い、スキャン速度5mm/sで、30回連続スキャニング加工する様式であり、角度のように、焦点域形状の影響を受けやすい部位ではダレが生じやすいと考えている。
以上より、3次元マイクロパターン形成に関しては、一定のパワー投入量での加工ではユニット形状中の急峻度確保は難しく、焦点域形状とパワー投入率を最適化することから検討をはじめる必要がある。
2-3-3.多次元パターン化した型技術の提案
ここでは、本年度開発した微細パターン転写モールド成形装置を用いて、2次元パターン金型の光学プラスチック試験片への転写成形実験を行い、その転写精度について検討する。転写成形素材は、代表的な光学プラスチック材であるPMMA(ポリ・メチル・メタ・アクリレート)である。
(1)微細パターン転写モールド成形装置
マイクロパターン形成した金型を用いて、そのパターンの光学プラスチック、光学ガラスあるいは金属シートなどに転写成形するには、モールド内のキャビティーも含め周辺空間を真空排気し、空気成分を排除した上で所定温度まで昇温し、モールドプレス成形し、冷却後、パターン転写したサンプルを取り出す、成形装置が不可欠である。ここでは、マイクロパターン形成金型が小型であり、かつモールドプレス荷重が最大でも数10kNであることなどを考え、高精度かつテーブルトップでモールドプレス成形を実施できる微細パターン転写モールド成形装置を設計、製作した。写真2.20にその外観を示す。
①はモールドプレス本体、②はプレス荷重制御系および電源、③は超高周波IH加熱制御系および電源、④は制御パネルおよびデータモニター、⑤はプレス成形スイッチ、⑥は超高周波IH加熱装置。
この装置の特徴は、1)CNC制御によるモールドプレス成形装置ゆえに、負荷方向のストローク精度は0.1µmとなり、高精度でのパターン転写が可能となる、2)真空排気を100Pa以下級まで実施するため、モールド内の残留気体の影響は無視できる、3)超高周波IHを利用しているため、加熱速度・冷却速度を制御できることに加え、所定温度保持を高精度で実施できる点にある。具体的には以下の仕様を満足している。
以下では、上記の仕様の第4番目に関して、より詳細に議論する。
表2.5の温度制御、加熱速度に関する仕様とも関連するが、モールド内の真空排気を行うとともに、超高周波IHを利用して適切な温度制御を実施するには、これまでの金型デザインを変更し、加熱部位を微細パターン転写に用いるモールドプレス型駒に限定する必要がある。ここでは、図2.12に示すように、微細パターン転写成形をシステム的に行うため、カセット金型を作成し、そこに真空排気系、超高周波IH加熱を行うように設計した。
第1に、真空排気系に関しては、カセット金型のモールドキャビティーのみの小空間を排気するように、カセット金型内の耐真空特性を向上させ、10秒以下程度で、キャビティー内を100Pa以下級に排気できるように設計、製作した。第2の超高周波IHによる温度制御系に関しては、写真2.20のように、超高周波加熱源はカセット金型外に設置し、IH加熱する水冷コイルのみを、真空圧力バウンダリーを介して、カセット金型内部に導入し、マイクロパターンを素材サンプルに転写する型駒のみを加熱するようにした。この設計により、加熱される物質体積が最小限となるため、成形中の所定温度保持の精度を向上できることに加え、冷却速度も大幅に向上させることができる。
(2)フレネルパターンの転写成形
微細パターン転写装置の成形性と精度を検証するため、光学素子の標準的なマイクロパターンであるフレネルパターンを利用して、パターン転写成形実験を行った。
写真2.21に、フレネルパターンを機械加工で形成後、DLCコーティングした転写成形用型駒を示す。機械加工によるマイクロパターン形成は、光学素子成形型技術では広く利用されており、ここでは、当該レーザー加工との転写成形挙動の比較の意味も併せて採用した。
機械加工後のレーザー反射測定装置(三鷹光機製)により求めた、パターン形状を図2.13に示す。
レーザー反射法による測定のため、フレネルパターンの段差部分で反射光が戻ってこないため、不連続なプロファイルになっているが、フラットな中心部から周辺にかけて高さ一定でピッチ寸法の異なる5つの円周グルーブパターンが形成されている。機械加工によるパターンニングでは、仕上げ切削後においても微小な加工パスは残存する。実際、この型駒について実測すると、図2.17のように、明瞭な表面粗さ分布が検出される。本研究で開発している装置がきわめて精密な転写を行うのであれば、図2.13に示したメインパターンと同様に、図2.14に示したメインパターン内部の微小な凹凸面も転写されるはずである。以下のPMMAへの転写成形実験では、この点も留意して実験を行った。
転写成形実験では、保持温度をPMMAのガラス転移点(105-110℃)直上の110-120℃、保持荷重を1kN、標準保持時間として保持時間を60sとした。成形後のPMMAレンズを写真2.22に示す。
写真2.21と比較すると、型駒形状が良好に転写されているように観察される。実際に、このPMMAレンズのメインパターンを計測すると、図2.15のようになる。これは図2.13と凹凸の関係で一致することがわかる。すなわち、本装置を用いて、型駒上のフレネルパターンがPMMA素材上に高精度に転写されていることがわかる。
水平方向の段差位置ならびにグルーブ深さが図2.13と良好に一致している。
次に、機械切削によるパターン形成時に生じる加工パス起源の粗さの転写性について調査してみよう。写真2.23に、転写成形したPMMAレンズの光学顕微鏡写真を示す。
フレネルパターンに対応するメインパターン以外に、各フレネルグルーブ内に、規則的な円周グルーブが観察される。そのピッチから、これは図2.10で示した加工パスによる表面粗さが転写成形されて生じたパターンであることがわかる。実際、PMMAレンズの詳細な粗さ分布を測定すると、図2.16に示すように、図2.14ときわめて相関性が高いことがわかる。
以上より、本転写成形装置は、機械加工による加工パス粗さも転写成形することができることから、µmレンジの規則的なマイクロパターンも精度よく転写成形することが期待される。
(3)V字グループパターンの転写成形
3次元パターン形成した金型(写真2.16、2.17)により、同じくPMMA材への転写成形を試みた。GC型材には、V字パターンが刻印させているため、PMMA材上には、V字状の凸パターンが規則的に形成されることが想定される。成形後のPMMA材の光学顕微鏡写真(低倍率)を写真2.24に示す。
微細V字パターンが規則的に転写されていることがわかる。さらに詳細な形状寸法を比較するため、光学顕微鏡の高倍率写真を、写真2.25に示す。
写真2.16、図2.7に対応するV字パターンに対応するパターンが高精度で、PMMA素材上に転写成形できていることがわかる。このことから、レーザー加工により形成した微細パ ターンを有するGC型材、DLCコーテッド型材あるいはSiC型材を用いて、当該真空モールドプレス成形装置により、種々の微細パターンを転写成形した、光学プラスチックレンズあるいは光学ガラスレンズを生産するプロセスを開発できる。
3.全体総括
3-1.研究開発の成果および課題
3-1-1.研究開発の成果
ピコ秒レーザーの位置制御機能、高精度回転制御装置、最適光学系の整備、あわせて加工環境浄化装置の整備を行ない、ファインセラミックスなどへの高精度・高速の1次元加工、2次元穴配置の高再現性を実現することが出来た。また、一定の形状ではあるが、周期的な多次元パターンの形成も可能になった。
3-1-2.今後の課題
光学ガラス素子および光学プラスチック素子のモールド成形用金型では、より複雑なパターン形状からなる3次元形状加工が、強く求められている。特殊なナノ精度の機械加工でも切削が困難なGC材、SiC材などを、高温安定な金型材質として選択するため、本研究開発したレーザー多次元加工が注目されている。この金型などにおける3次元形状加工では、急峻な面と隣接面角度保持、平滑な面精度が求められる。今回の研究では、このような形状形成に充分な技術的成果を得るまでに至らなかった。これは研究開発中で見出したように、ビーム制御法、加工パスの設計などに関して、まだ研究開発が不足していることに加え、CAMとして十分にハードウエア機能・機構を利用しつくしていないことにも、大きな問題点がある。
しかしながら、今回の研究で得られた高精度の制御装置は、3次元加工における種々の問題点を解決する空間ポジショニング制御技術の実現、展開に適しており、今後の研究開発における基盤技術力整備において、威力を発揮するものと考えている。特にエッチング法、機械加工法ではパターン形成が困難な高硬度材へのマイクロパターン形成に対して、レーザーでの加工法確立の研究を継続的に進める必要がある。
またGC材で見出したように、パワー出力比が1%程度であっても、十分な2次元、3次元加工を検討できることは、光学ガラス素子のモールド金型において、より出力の小さいピコ秒あるいはサブピコ秒レーザーでの加工の可能性を示唆しており、今後の基盤技術力整備にも活用したい。
さらに今回はGC材のみに限定して検討したが、DLCコーティング膜にも適用可能であり、今後は、種々の基材材料上にコーティングDLC膜への多次元パターン形成も行い、本加工法の有効性を展開していきたい。
3-2.事業化展開
8月よりプローブカードメーカー、自動車メーカーにサンプル出荷を開始した。
その他、自動車部品メーカー、繊維ノズルメーカーなどからの量産依頼が相次いでいるために、ピコ秒レーザー位置制御装置を、新規に2台設備予定である。9月までの完成を目指している。