超短レーザーパルスによる金属表面への微細周期構造の形成
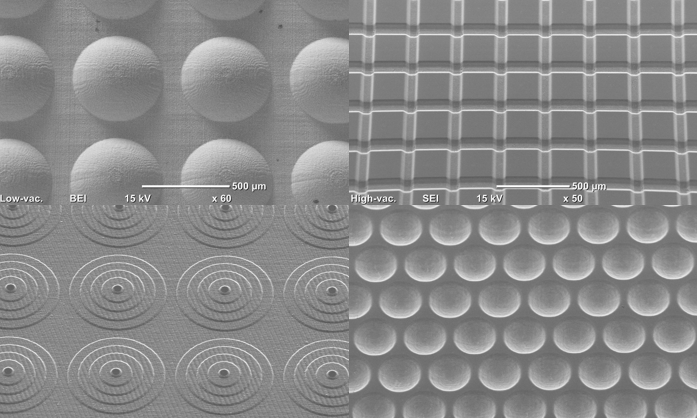
レーザー学会誌 レーザー研究
The Review of Laser Engineering
超短レーザーパルスによる金属表面への微細周期構造の形成
小清水 大介1,小俣 恵一1,草野 浩1,副田 精次郎1,井ノ原 忠彦1,松岡 芳彦2
1(株)リプス・ワークス( 〒144-0033 東京都大田区東糀谷6-4-17 OTAテクノCORE)
2(株)実用技術研究室( 〒192-0014 東京都八王子市みつい台2-5-7)
Fabrication of Periodical Micro-tructure on Metal Surface Using Ultra-Short Laser Pulses
Daisuke KOSHIMIZU,1 Keiichi OMATA,1 Hiroshi KUSANO,1 Seijirou SOEDA,1 Tadahiko INOHARA,1 and Yoshihiko MATSUOKA2
1L. P. S. Works co., ltd., OTA Techno CORE, 6-4-17 Higashikoujiya, Ota-ku, Tokyo 144-0033
2Practical Technology Laboratory, Inc., 2-5-7 Mitsuidai, Hachioji, Tokyo 192-0014
(Received July 9, 2013)
Precision machining industry requires practical technology for non-thermal processing. Using green ps laser pulses, we examined periodical micro-fabrication on the Cu plate surface. The diameter of the formed dimple was about 35 μm and around 10 μm depth. We observed no remarkable heat damage, such as discoloration, melting, or re-solidifi cation. The dispersion of the processing size was reduced by avoiding thermal damage. We achieved a processing amount of about 300 dimple/s.
Key Words: Micro-processing, Ultra-short pulse laser, Periodical micro-structure, Dimple
1.はじめに
数多くの生産現場で,レーザー加工装置が導入され,いろいろな種類の製品が製造されている.レーザーが生産現場に導入された初期の時代は,レーザー光のエネルギーを熱源として用いる「熱加工」が主流であった1).溶融させることにより材料に形状を付与する「熱加工」では,溶融・再凝固を経るために,加工部の寸法は少なからぬばらつきを生じる.製品や部品の加工寸法がmmオーダーであれば,レーザー加工後の寸法は,ほぼ要求公差内に抑え込むことが可能である.一方,要求公差が小さくなってくると,「熱加工」に基づくレーザー加工では加工後の寸法を公差内におさめることが極めて難しく なってくる.
パルスレーザーが開発され,レーザーパルス幅がns領域に入ってくると,アブレーション2)と呼ばれる溶融状態を経ない材料除去が可能となり,レーザーによる材料への精密な形状付与加工の実現が期待された.しかしながら,「非熱加工」であるアブレーションは,加工閾値近傍のパルスフルーエンスのみで実現可能であり,且つ,その条件下での材料の除去率は極めて小さい.材料の除去率を高めるためにパルスフルーエンスを大きくすると,加工が「熱加工」に基づくものに次第に変化していき,熱影響が無視できなくなるために,加工の寸法精度の精密化には限界があった.
半導体製造プロセスで活躍したエキシマレーザー3)はユニークな位置づけにある.レーザーパルス幅はμs領域にあり,材料と光の相互作用を考えると熱影響は無視できない.しかしながら,エキシマレーザーの繰返し周波数は数百Hz程度であり,パルス間隔は数ms程度になる.この長いパルス間隔の間に発生し熱が拡散するために,加工部での熱の蓄積が抑制され,熱影響が顕著とならない.
近年次々と新しいモデルが発表されているps,fsパルスレーザー4)は,工業的な「非熱加工」の実現が期待されている.パルス幅(パルス持続時間)が,材料と光の相互作用の結果として加工部に熱が発生する典型時間よりも短いために,適切な加工条件下では理想的な「非熱加工」が行えるものと考えられる5,6).
繰り返し周波数がMHz領域の超短パルスレーザーが利用可能になり,この高速加工性を印刷製版の直接加工に応用するための基礎検討がBrueningらにより報告されている7).彼らの加工手法はレーザーパルスの集光スポットを加工面上で走査するものであり,基本的には集光スポットはワーク加工面上を常時移動し続けており,従って熱的な影響を排除しやすい.一方で,小さく形成した集光スポットと同程度のサイズの窪み(ディンプル)を離散的にワーク面上に加工しようとする場合,特にディンプルの形状精度を求められる場合には,繰り返し走査的な手法よりも従来的なパーカッション加工の方が精度確保の点で実用的である.しかしながらパーカッション加工は,同一加工点に必要ショット数のレーザーパルスを連続照射するために,熱的な影響が出やすい問題がある.工業的な観点では,集光スポットサイズと同程度のサイズの微細形状を,熱影響を抑制して寸法精度良く加工可能であるのか,またその場合にどの程度の寸法精度が期待できるのかについて,興味が持たれる.
本報告では,psレーザーパルスを用いた加工においても熱影響が比較的出やすいパーカッション加工による金属材料表面へ周期微細構造付与における,加工形状の寸法精度を検討する.銅板への照射条件として,我々のこれまでの検討で熱影響を抑えることが確認できている条件(繰り返し周波数100 kHz,パルスフルーエンス約1.0 J/cm2 pulse)を用い,微細周期構造として銅板表面に
直径35µm程度のディンプルを,100µmピッチで形成する.また,加工所要時間の内容の解釈から,高スループット化について考察を行う.
2.実 験
レーザー発振器には,Light Conversion社製PHAROSを用いた.発振中心波長1028nmの第二高調波出力(中心波長514nm)を実験に用いた.出力ビームのM2は約1.1.パルス幅が190 fsから10 psの範囲で可変であるPHAROSを,10 psのパルス幅に調整した.また繰返し周波数は,可変範囲(single shot~600 kHz)内の100 kHzに設定した.
レーザービームの集光,走査には,SCANLAB社製intelliSCANと,焦点距離f = 100 mmのテレセントリック型のF-θレンズからなるガルバノスキャナを用いた.PHAROSからの出力ビームは,ビームエキスパンダを用いて,直径約3 mmのコリメート光とし,ガルバノスキャナに入力した.ガウシアンビームのレンズによる集光スポット直径d1/e2は,
d1/e2 = α M2 λ f / D1/e2 (2.1)
で与えられる2).ここで,α はF-θ レンズごとに与えられる比例係数,λは波長,D1/e2は入射ビームの直径(1/e2)である.実験に用いたF-θレンズの持つ比例係数αは約1.83である.従って,形成される集光スポットの直径d1/e2は約34µmである.
PHAROSから100kHzの繰返し周波数で出力されるパルスを,ワーク近傍に設置したパワーメーターで受け,計測される平均パワーが1.2 Wとなるように出力を調整した.このとき,レーザーパルス一つの持つパルスエネルギーは,12µJ/pulseになる.直径(1/e2)34µmの集光スポットの面積は約9.1 × 10‒6 cm2であり,集光スポット内のパルスフルーエンス2)は約1.1 J(/ cm2・pulse)である.
ワークには,銅(Cu)板を用いた.ワーク表面に集光ビームの焦点を合わせた.ガルバノスキャナの制御系は,ガルバノモーターを制御するとともに,レーザー発振器の出力もあわせて制御する.本検討では,ワーク上にレーザーパルスの加工点を,100µmピッチで千鳥子(三角格子)状に1024点設定した.ガルバノスキャナを用いて設定された加工点に順次集光スポットを移動させては,所定のレーザーパルスを照射する手順を繰り返した.
加工点に照射するレーザーパルスは,50ショット,100ショット,200ショットの3つの場合を実施した.集光スポットを移動させるためのガルバノスキャナの設定パラメータは,ジャンプスピード100 mm/s,ジャンプディレイ200µsである.ジャンプスピードとは,加工点から加工点へ集光スポットを移動させるときの,ワーク面上での集光スポットの移動速度,またジャンプディレイとは,移動後の集光スポットの振動が許容値以下に収まるまでの待ち時間である.加工後の表面を走査電子件顕微鏡で観察するとともに,そのサイズを測定顕微鏡(オリンパス社製,STM5-UM,計測精度0.1 µm)を用いて計測・評価した.
3.結 果
加工点あたり200ショットのレーザーパルスを照射して,銅(Cu)板に形成されたディンプルの走査電子顕微鏡写真を,Fig. 1に示す.またTable 1に,形成されたディンプル形状の平均サイズをまとめる.さらに,加工点あたり200ショットのレーザーパルスを照射した場合の,任意の24点を計測した寸法の標準偏差などをTable 2に示す.
照射ショット数の増加に伴い,形成されるディンプル深さもほぼ比例して増大している.ディンプルの直径は,照射した集光スポット直径にほぼ等しい.また,照射ショット数が大きくなると,形成されるディンプル直径は若干大きくなっている.
1024点のディンプル形状加工に要した時間は,1加工点あたり50ショット照射の場合2.7 s,100ショット照射の場合3.2 s,200ショット照射の場合4.2 sであった.
4.考 察
パルス幅10ps,波長514nmのレーザーパルスを用いた加工においても熱影響が比較的出やすいパーカッション加工による,銅(Cu)板表面への約35µm直径のディンプル形状の周期的形成における,加工形状の寸法精度を検討した.
Fig. 1に明瞭に示されているように,加工後のワーク表面には,顕著な変色や溶融などの熱影響は現れていない.この結果は,パルス幅が数十nsの一般的な半導体励起固体(DPSS)パルスレーザーを用いた同様の加工結果に,著しい変色やバリなどの溶融痕が現れるのと対照的である.波長やパルス幅によって変化するが,例えばJandeleitらによる報告では,波長1053nmパルス幅40ps のレーザーパルス照射による銅(Cu)の加工閾値は0.2 J/cm2 pulse程度である8).我々が用いたパルスフルーエンス1.1 J/cm2pulseは,熱影響の抑制と加工のスループットのバランスから選んだ値である.他の材料における加工経験を加えて考えると,psレーザーパルスを用いた加工においても熱影響が比較的出やすいパーカッション加工では,パルスフルーエンスは加工閾値の数倍程度に抑えることで,非熱的な加工が実現できるものと考えられる.
非熱的な加工の実現により,加工部に溶融・再凝固の痕は見られず,加工部のエッジは極めて鮮明である.このことは,加工寸法精度の向上に良い影響を与えている.Table 2に示されているように,200ショットのレーザーパルスで形成された直径が約35µm,深さが約10µmの24個のディンプルの寸法の計測値から算出した標準偏差σは,y軸方向に沿った直径の値で0.38µm,深さで0.55µmに留まっている.ばらつきの範囲の指標として± 3σ を用いると,1024個のディンプルのサイズは,
Dx: 34.9 ± 3.32µm
Dy: 34.3 ± 1.13µm
Depth: 10.1 ± 1.64µm
の範囲にあると推定される.x軸方向に沿ったディンプルの直径Dxは,ばらつきの範囲が他に比べて若干大き い.後に議論するように,x軸方向は,加工点を順次移動させるためのガルバノスキャナの主走査方向であり,駆動・停止が頻繁に生じる.これによるガルバノミラーの振動が許容値以下に減衰するまでの待ち時間がジャンプディレイと呼ばれるパラメータである.ジャンプ後のガルバノミラーの完全静止には長い時間が必要であり,完全静止を待って次の加工を行うことは実用的でない.実際上は,加工サイズの広がりが許容範囲内になるようなガルバノミラーの残存振動となるように,ジャンプディレイを調整する.この調整により,x軸方向に沿ったディンプル直径Dxの寸法のばらつきは,さらに抑え込めるものと考えられる.
レーザーパルスによるパーカッション加工における加工直径および加工深さは,照射するパルス数,パルス幅,パルスフルーエンスに依存することが報告されている8‒11).本実験の場合,パルス幅と,照射パルス数は固定であるので,y軸方向に沿った直径の値および深さのばらつきは,主にパルスエネルギーのショット毎のばらつきによるものと推測される.
加工点を順次移動させるについては,ガルバノスキャナを用いて,Fig. 2のような経路で銅(Cu)板上の集光スポットを走査した.左から右に順番に32点加工した後,次の行に移る際には左端まで移動させる,いわゆる一方向走査を行った.1024点加工する間の,ひとつの加工点あたりの集光スポットの走査に要した平均的な時間は,1.94 msと計算される.ひとつの加工点あたり200ショット照射した場合,1024点の加工に要した時間は4.2 s,従ってひとつの加工点あたりに要した時間は4.10 ms,ジャンプディレイは一回の移動ごとに0.20 ms,200ショットの照射に要する時間は2.00 msである.
4.10 ms≒1.94 ms + 0.20 ms + 2.00 ms
すなわち,ひとつの加工点あたり200ショット照射した場合,加工時間の半分を集光スポットの移動に,残りの半分をレーザーパルスの照射に用いていることが理解できる.レーザーパルスの照射が加工の主体であるから,これを削減することは難しい.従って,所用加工時間を短縮の方策は,先ず集光スポットの移動に要する時間の短縮に求めることになる.
すぐに考えつくのは,一方向走査ではなく,双方向走査にすることである.これをFig. 3に示す.右端まで走査した後に左端まで戻ることがなくなったので,ひとつの加工点あたりの集光スポットの走査に要する平均的な時間は1.00msになる. この場合のひとつの加工点あたりに要する加工時間は,
3.20 ms = 1.00 ms + 0.20 ms + 2.00 ms
と推定される.
我々が実施した一方向走査では,ひとつの加工点あたり200ショット照射した場合の単位時間当たりの加工ディンプル数は,1/0.0041≒244ディンプル/sである.集光スポットの走査を双方向に変えることで,1/0.0032≒313ディンプル/sへと単位時間当たりの加工ディンプル数を増大させることが可能である.
5.まとめ
psレーザーパルス(パルス幅10 ps,波長514nm)を用いた加工においても熱影響が比較的出やすいパーカッション加工による,金属材料表面へ周期微細構造付与における,加工形状の寸法精度を検討した.
銅(Cu)板表面へ,パルスフルーエンス1.1 J(/ cm2・pulse)の条件で,約35µm直径のディンプルを100 µmピッチの千鳥格子で周期的に1024個形成した.加工されたワーク表面には,顕著な変色や溶融などの熱影響は現れていない.熱影響が出やすいパーカッション加工では,加工閾値の数倍程度のパルスフルーエンスに抑えることで,熱影響の抑制と加工のスループットの両立の実現が期待できる.
熱影響の大幅な抑制は,加工寸法精度の向上に良い影響を与えている.直径約35µm,深さ約10µmのディンプルのパーカッション加工において,ガルバノスキャナによる走査方向と直交方向のディンプル直径及びディンプル深さの寸法のばらつきは,3σ = 1.1~1.6 µmであった.ガルバノスキャナによる走査方向と平行な方向のディンプル直径の寸法のばらつきは,3σ = 3.3 µmと他に比べると若干大きい.これは次の加工点へとガルバノミラーを動かした際に発生するガルバノミラーの残存振動によるものと推測され,ジャンプディレイの最適化でさらに抑えられると考えられる.
謝 辞
本研究は平成25年度戦略的基盤技術高度化支援事業(サポイン)「空間位相制御レーザー加工によるマイクロテクスチュア技術の開発」により行われた成果です.
参考文献
1) 金岡 優:絵ときレーザー加工の実務( 日刊工業新聞社, 2007).
2) 松岡 芳彦:OPTRONICS 31( 2012) No.361, p.134.
3) 黒澤 宏:レーザー基礎の基礎( オプトロニクス社,2003) p.86.
4) A . Ostendorf:レーザー研究 30( 2002) 221.
5) 松岡 芳彦:OPTRONICS 31( 2012) No.364, p.191.
6) 松岡 芳彦:OPTRONICS 31( 2012) No.369, p.158.
7) S. Bruening, G. Henning, S. Eifel, and A. Gillner : Physics Procedia 12 (2011) 105-115..
8) J. Jandeleit, G. Urbadch, H. D. Hoffmann, H.-H. treusch, and E. W. Kreutz: App. Phys. A 63 (96) 117-121.
9) B. N. Chichkov, C. Momma, S. Nolte, F. von Alvensleben, and A. Tünnermann: Appl. Phys. A 63 (96) 109-115.
10) S. Nolte, C. Momma, H. Jacobs, A. Tummermann, B. N. Chichkov, B. Wellegehausen, and H. Welling: J. Opt. Soc. Am. B 14 (97) 2716-2722.
11) S. Preuss, A. Demchuk, and M. Stuke: Appl. Phys. A 61 (95) 33-37.